ถาดไข่มีบทบาทสำคัญในการบรรจุและการขนส่งไข่ ทำให้จำเป็นในฟาร์ม ซูเปอร์มาร์เก็ต และอุตสาหกรรมแปรรูปอาหาร
ถาดไข่ทำจากวัสดุที่เป็นมิตรต่อสิ่งแวดล้อม เช่น เยื่อกระดาษและเศษกระดาษ กันกระแทก เป็นมิตรกับสิ่งแวดล้อม และรีไซเคิลได้ง่าย ด้วยความต้องการถาดไข่ที่เพิ่มขึ้นในตลาด การปรับปรุงประสิทธิภาพการผลิตและการรับรองคุณภาพของผลิตภัณฑ์จึงกลายเป็นจุดสนใจหลักสำหรับธุรกิจ
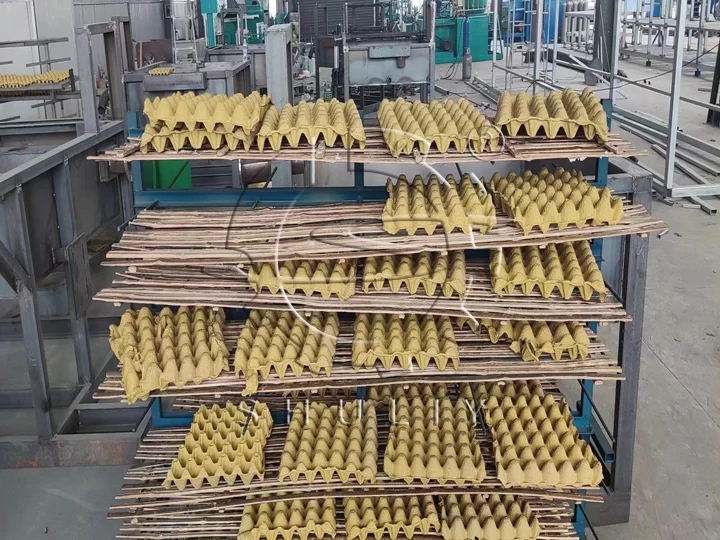
โอกาสทางการตลาดสำหรับการผลิตถาดไข่
ด้วยการบริโภคไข่ที่เพิ่มขึ้นทั่วโลก ความต้องการถาดใส่ไข่ก็เพิ่มขึ้นอย่างต่อเนื่องเช่นกัน นอกจากนี้ ความตระหนักที่เพิ่มขึ้นเกี่ยวกับการคุ้มครองสิ่งแวดล้อมและความกังวลด้านความปลอดภัยของอาหารทำให้ผู้บริโภคนิยมถาดไข่ที่เป็นมิตรกับสิ่งแวดล้อม
เพื่อปรับตัวให้เข้ากับแนวโน้มนี้ บริษัทต่างๆ จะต้องปรับปรุงประสิทธิภาพการผลิตอย่างต่อเนื่องและลดต้นทุนเพื่อให้สามารถแข่งขันในตลาดได้
ด้วยการปรับปรุงกระบวนการผลิตและการเพิ่มประสิทธิภาพขั้นตอนการทำงาน ธุรกิจสามารถตอบสนองความต้องการของตลาดในขณะเดียวกันก็ส่งมอบผลิตภัณฑ์คุณภาพสูงและเป็นมิตรกับสิ่งแวดล้อม ดังนั้นจึงรักษาตำแหน่งที่แข็งแกร่งในตลาดที่มีการแข่งขันสูงขึ้น
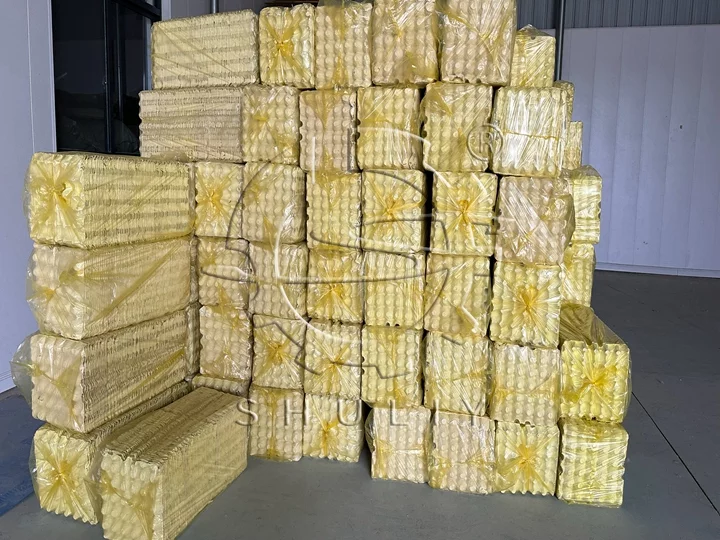
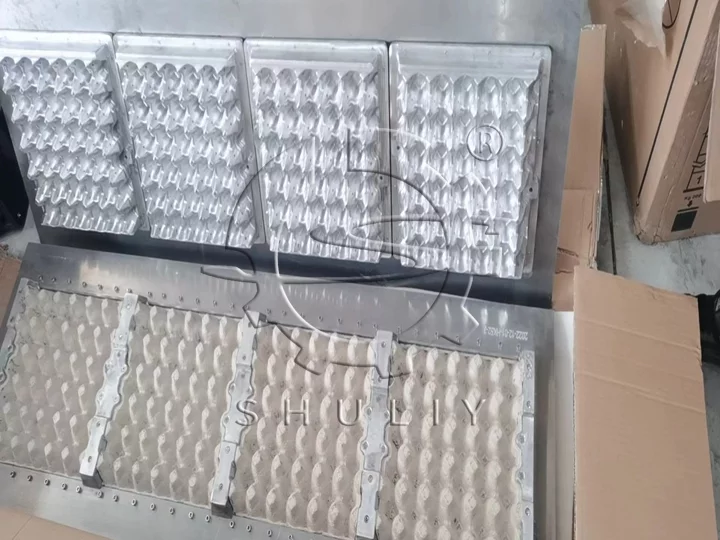
ประเภทของอุปกรณ์การผลิตถาดไข่
เพื่อให้บรรลุการผลิตที่มีประสิทธิภาพ โดยทั่วไปสายการผลิตถาดไข่จะประกอบด้วยอุปกรณ์หลายประเภท ได้แก่:
- เครื่องปั่นเยื่อ. ใช้ในการผสมกระดาษรีไซเคิลและน้ำให้เป็นเยื่อ.
- เครื่องขึ้นรูป. สร้างรูปเยื่อให้เป็นถาดไข่.
- เครื่องอบแห้ง. อบแห้งถาดไข่ที่ขึ้นรูปเพื่อให้แน่ใจว่ามีความแข็งแรง.
- เครื่องอัดร้อน. อัดถาดไข่ให้แน่นขึ้นเพื่อเพิ่มความทนทาน.
- เครื่องบรรจุ. จะจัดเรียง, คัดแยก, และบรรจุถาดไข่ที่เสร็จแล้วโดยอัตโนมัติ เพื่อความสะดวกในการขนส่งและจัดเก็บ.
ด้วยการกำหนดค่าอุปกรณ์เหล่านี้อย่างเหมาะสม จึงสามารถเพิ่มประสิทธิภาพการผลิตได้อย่างมีประสิทธิภาพ บริษัทสามารถเลือกเครื่องจักรแต่ละเครื่องหรือสายการผลิตทั้งหมดได้ตามความต้องการในการผลิต
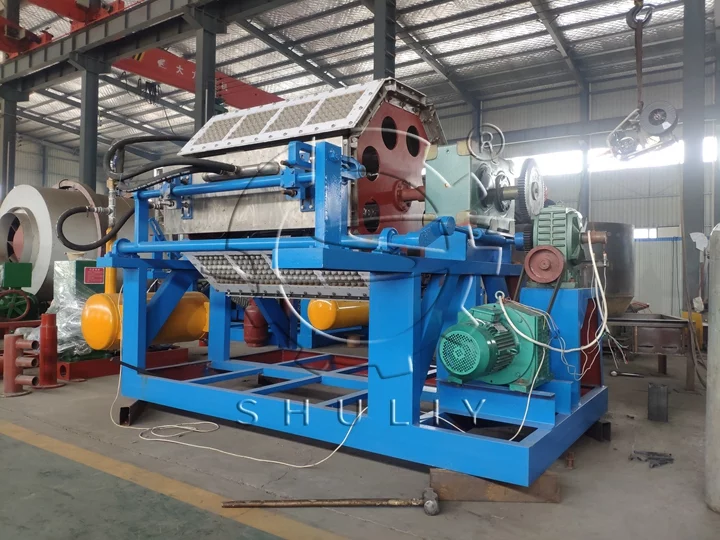
นอกเหนือจากการเลือกอุปกรณ์แล้ว การเลือกวัตถุดิบที่เหมาะสมยังเป็นสิ่งสำคัญในการเพิ่มประสิทธิภาพการผลิตอีกด้วย
ปัจจัยสำคัญในการปรับปรุงประสิทธิภาพการผลิตถาดไข่
1. คัดสรรวัตถุดิบคุณภาพสูง
รากฐานของการผลิตถาดไข่ที่มีประสิทธิภาพเริ่มต้นจากการเลือกวัตถุดิบที่เหมาะสม เศษกระดาษและกระดาษแข็งที่สะอาดเหมาะอย่างยิ่งเนื่องจากเยื่อกระดาษง่ายกว่าและมีคุณสมบัติการยึดเกาะที่ดีเยี่ยม
เพื่อให้แน่ใจว่าความสม่ำเสมอของเยื่อกระดาษเหมาะสมที่สุดสำหรับการขึ้นรูปถาดไข่ที่ทนทานและมีคุณภาพสูง การใช้วัสดุที่มีสิ่งเจือปนน้อยที่สุดถือเป็นสิ่งสำคัญ เนื่องจากสิ่งเจือปนอาจทำให้ถาดอ่อนแอลงและขัดขวางกระบวนการผลิต
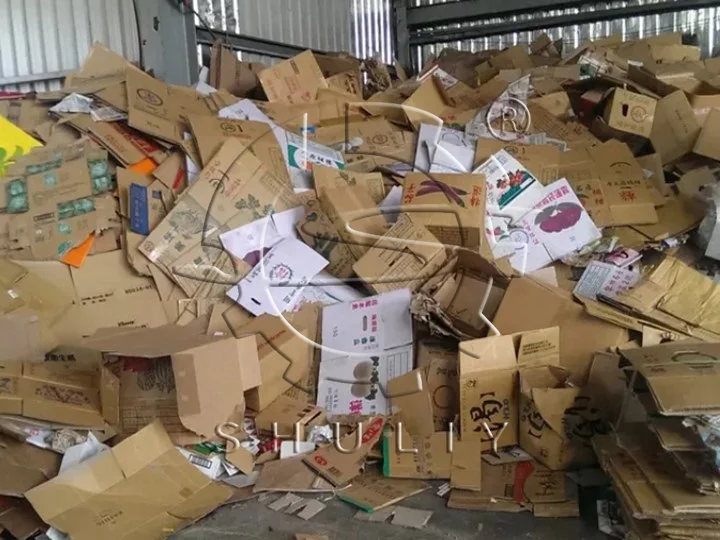
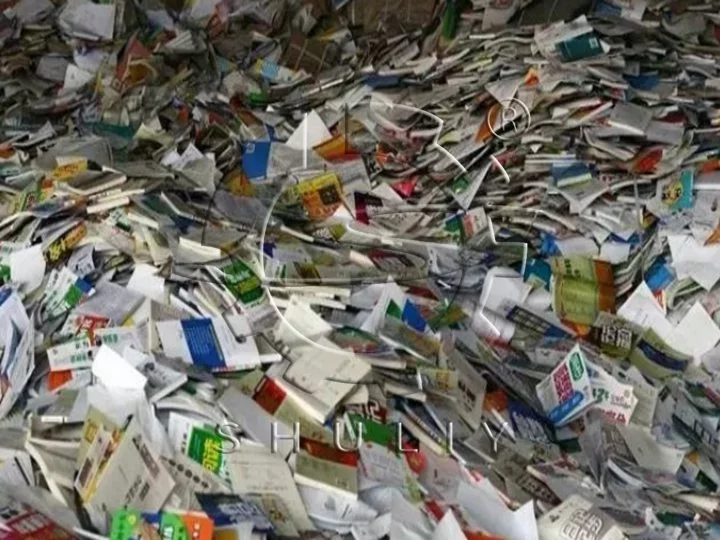
2. เพิ่มประสิทธิภาพการเลือกอุปกรณ์และเค้าโครงไซต์
การผลิตที่มีประสิทธิภาพไม่ใช่แค่การมีอุปกรณ์ที่ดีเท่านั้น แต่ยังเกี่ยวข้องกับการจัดวางอุปกรณ์เชิงกลยุทธ์และการจัดวางสถานที่ นอกจากนี้ สิ่งอำนวยความสะดวกการระบายอากาศและการปกป้องสิ่งแวดล้อมที่ดีสามารถปรับปรุงคุณภาพของสภาพแวดล้อมการผลิต เพื่อให้มั่นใจในความปลอดภัยและความยั่งยืน
ต่อไป เราจะแนะนำวิธีปรับปรุงการผลิตถาดไข่ของคุณ
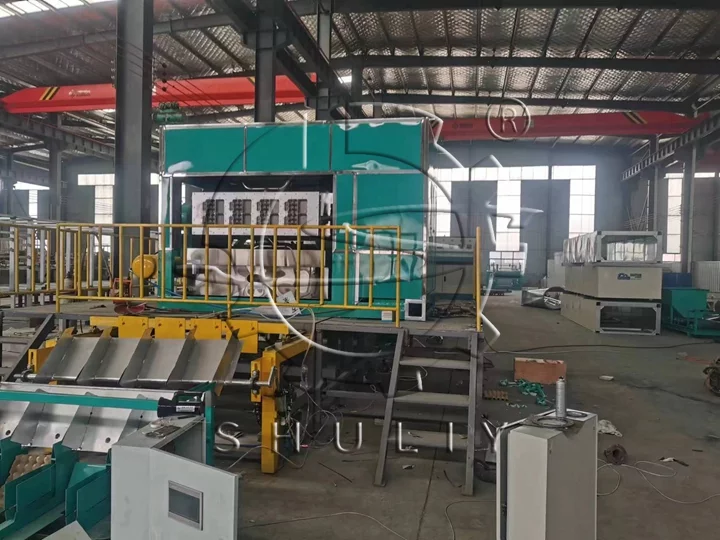
การเพิ่มประสิทธิภาพกระบวนการผลิตกล่องกระดาษ
เพื่อเพิ่มประสิทธิภาพสูงสุดในการผลิตถาดไข่ การกลั่นกระบวนการต้องอาศัยมากกว่าเครื่องจักรคุณภาพสูง แนวทางที่มีโครงสร้างเพื่อให้ได้ประสิทธิภาพสูงสุดมีดังนี้
1. เค้าโครงอุปกรณ์เชิงกลยุทธ์
- จากการปั่นไปยังการขึ้นรูป. วางเครื่องปั่นเยื่อใกล้กับเครื่องขึ้นรูป เพื่อให้ระยะทางที่เยื่อต้องเดินทางสั้นลง ลดเวลาในการขนส่งและการใช้พลังงาน.
- จากการขึ้นรูปไปยังการอบแห้ง. วางเครื่องอบแห้งทันทีหลังจากเครื่องขึ้นรูป การตั้งค่านี้ช่วยให้การเปลี่ยนแปลงจากขั้นตอนเปียกไปยังขั้นตอนแห้งเป็นไปอย่างราบรื่น ลดการจัดการที่ไม่จำเป็นและความล่าช้าที่อาจเกิดขึ้น.
การจัดวางอุปกรณ์ที่มีประสิทธิภาพช่วยรักษาการไหลอย่างต่อเนื่อง ลดการหยุดชะงัก และเพิ่มความเร็วในการผลิตโดยรวม
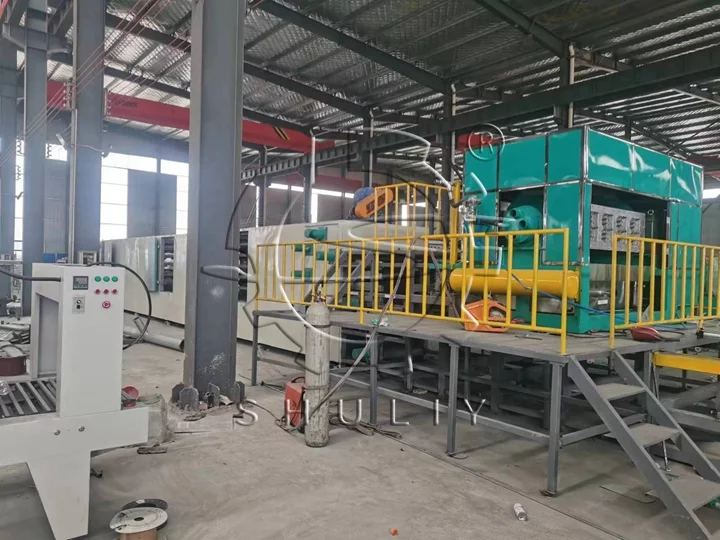
2. การบำรุงรักษาอุปกรณ์อย่างสม่ำเสมอ
- การตรวจสอบตามกำหนดเวลา. ตรวจสอบเครื่องจักรที่สำคัญเช่นปั๊มสุญญากาศและระบบขึ้นรูปอย่างสม่ำเสมอ การตรวจสอบเป็นประจำช่วยป้องกันการเสียหายที่ไม่คาดคิด.
- การซ่อมแซมที่ทันเวลา. แก้ไขปัญหาด้านการบำรุงรักษาอย่างรวดเร็วเพื่อหลีกเลี่ยงการหยุดการผลิตและยืดอายุการใช้งานของเครื่องจักร วิธีการเชิงรุกนี้ช่วยให้มั่นใจในคุณภาพผลิตภัณฑ์ที่สม่ำเสมอและลดเวลาที่หยุดทำงาน.
การบำรุงรักษาตามปกติถือเป็นสิ่งสำคัญสำหรับการทำงานที่ราบรื่นและผลผลิตคุณภาพสูง
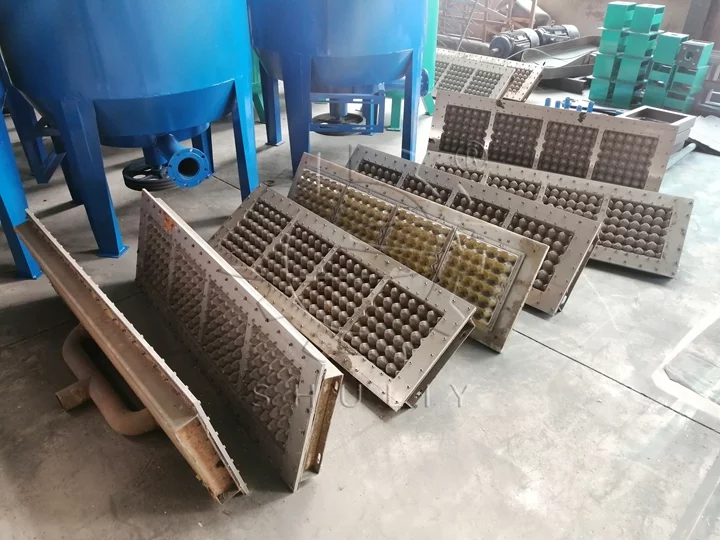
3. การจัดสรรบุคลากรอย่างมีประสิทธิภาพ
- ผู้ปฏิบัติงานที่มุ่งมั่น. มอบหมายผู้ปฏิบัติงานเฉพาะให้แต่ละขั้นตอนของสายการผลิต—การปั่น, การขึ้นรูป, และการอบแห้ง. เจ้าหน้าที่เฉพาะทางสามารถจัดการส่วนของตนได้อย่างมีประสิทธิภาพและแก้ไขปัญหาได้อย่างรวดเร็ว.
- การแก้ปัญหา. ฝึกอบรมบุคลากรให้สามารถระบุและแก้ไขปัญหาเล็กน้อยได้อย่างรวดเร็วเพื่อป้องกันการหยุดชะงักที่สำคัญ วิธีการจัดสรรบุคลากรที่มุ่งเน้นนี้ช่วยให้แต่ละส่วนของกระบวนการผลิตทำงานได้อย่างราบรื่น.
การจัดสรรบุคลากรอย่างเหมาะสมทำให้มั่นใจได้ว่าแต่ละขั้นตอนการผลิตจะได้รับการตรวจสอบอย่างใกล้ชิด ซึ่งจะช่วยเพิ่มประสิทธิภาพและคุณภาพของผลิตภัณฑ์
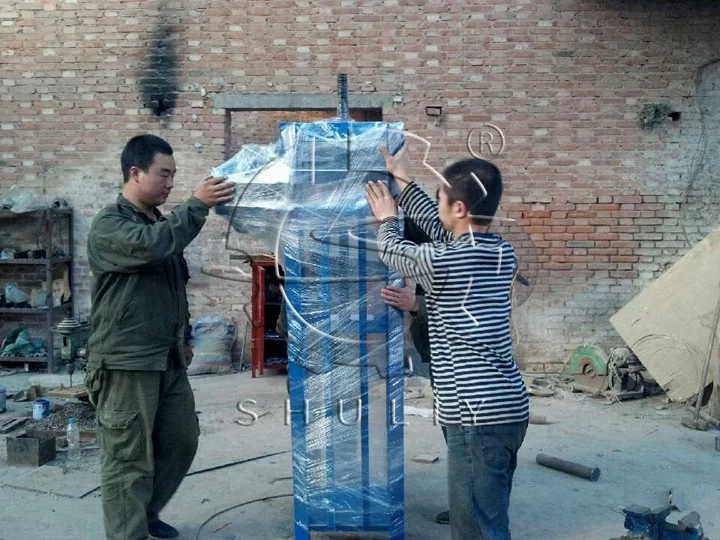
ด้วยการผสานรวมโครงร่างอุปกรณ์เชิงกลยุทธ์ การบำรุงรักษาที่เข้มงวด และบุคลากรที่ได้รับการจัดสรรอย่างดี คุณสามารถเพิ่มประสิทธิภาพกระบวนการผลิตถาดไข่ให้เหมาะสม ตอบสนองความต้องการของตลาดในขณะที่ยังคงรักษามาตรฐานคุณภาพสูงไว้ได้
ข้อกำหนดทางเทคนิคสำหรับถาดไข่คุณภาพสูง
การผลิตถาดไข่คุณภาพสูงเป็นมากกว่าการมีอุปกรณ์การผลิตที่เชื่อถือได้และการจัดการที่มีประสิทธิภาพ แต่ยังต้องปฏิบัติตามมาตรฐานทางเทคนิคเฉพาะเพื่อให้มั่นใจถึงความทนทานและฟังก์ชันการทำงาน ข้อกำหนดทางเทคนิคที่สำคัญสำหรับการผลิตถาดไข่คุณภาพเยี่ยมมีดังนี้
1. ปริมาณความชื้นที่เหมาะสม
การรักษาระดับความชื้นที่ถูกต้องเป็นสิ่งสำคัญในการผลิตถาดไข่ ควรควบคุมปริมาณความชื้นของเยื่อกระดาษระหว่าง 50-60% ในระหว่างขั้นตอนการเยื่อกระดาษเพื่อช่วยให้การขึ้นรูปและการขึ้นรูปเหมาะสม หลังจากการปั้น ควรลดความชื้นของถาดไข่ให้ต่ำกว่า 10% เพื่อให้แน่ใจว่าแห้งเพียงพอและแข็งแรงเพียงพอสำหรับการจัดการและขนส่ง
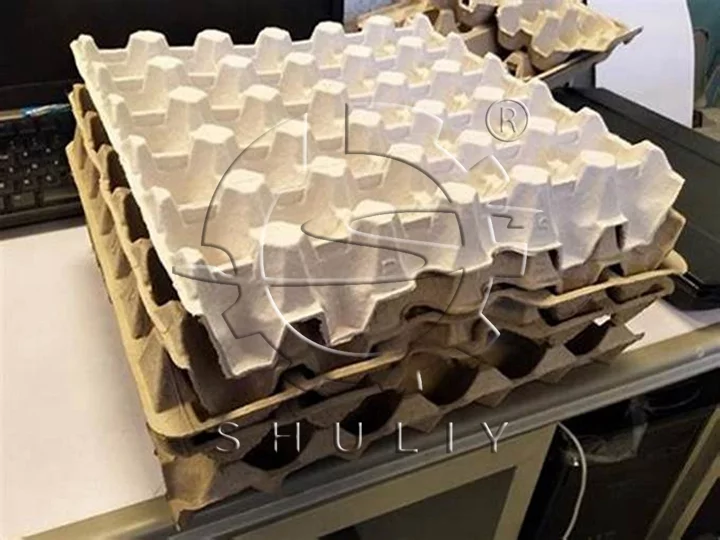
2. ความหนาสม่ำเสมอ
ความหนาสม่ำเสมอทั่วทั้งถาดไข่ทั้งหมดถือเป็นสิ่งสำคัญเพื่อให้มั่นใจถึงความสามารถในการดูดซับแรงกระแทก ความหนาที่สม่ำเสมอช่วยกระจายน้ำหนักได้เท่าๆ กัน ช่วยปกป้องไข่ระหว่างการขนส่งได้ดีขึ้น ความหนาที่สม่ำเสมอยังช่วยลดโอกาสที่จะเกิดจุดอ่อน ซึ่งอาจนำไปสู่การแตกหักหรือการเสียรูปภายใต้ความเครียด
3. กำลังรับแรงอัดสูง
ถาดไข่ต้องมีกำลังรับแรงอัดสูงเพื่อทนทานต่อแรงกดดันที่เกิดขึ้นระหว่างการวางซ้อน การขนย้าย และการขนส่ง ถาดไข่ที่แข็งแรงช่วยป้องกันไข่ไม่ให้เสียหายหรือแตก ช่วยให้ส่งถึงที่หมายได้อย่างปลอดภัย การบรรลุถึงระดับความแข็งแกร่งนี้จำเป็นต้องมีการควบคุมกระบวนการขึ้นรูปและการอบแห้งอย่างระมัดระวัง เพื่อหลีกเลี่ยงจุดอ่อนหรือข้อบกพร่อง
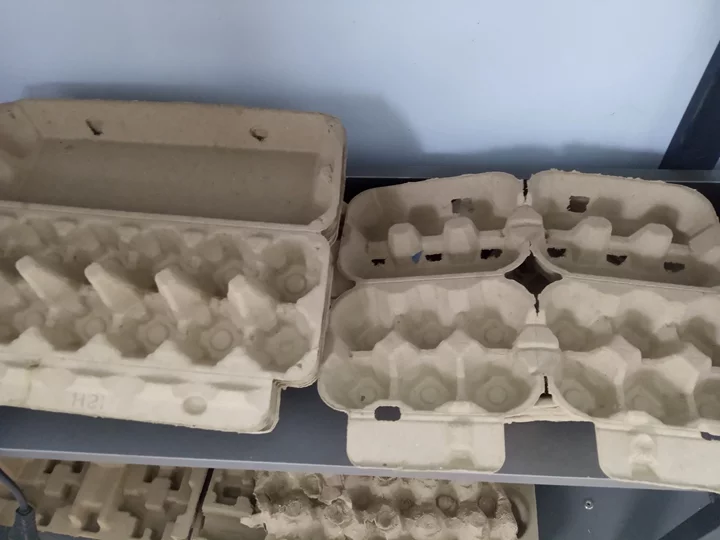
การปฏิบัติตามข้อกำหนดทางเทคนิคเหล่านี้ ผู้ผลิตสามารถผลิตถาดไข่ที่มีประสิทธิภาพและความน่าเชื่อถือที่เหนือกว่า ปกป้องเนื้อหาในถาดได้อย่างมีประสิทธิภาพ ขณะเดียวกันก็รักษาความสมบูรณ์ของโครงสร้างตลอดห่วงโซ่อุปทาน
หลักการทำงานและกระบวนการผลิตของเครื่องถาดไข่
การทำความเข้าใจหลักการทำงานของเครื่องถาดไข่ถือเป็นสิ่งสำคัญสำหรับการดำเนินงานและบำรุงรักษาอุปกรณ์การผลิตอย่างมีประสิทธิภาพ กระบวนการผลิตของเครื่องถาดไข่ประกอบด้วยสามขั้นตอนหลัก: การผลิตเยื่อกระดาษ การปั้น และการอบแห้ง ด้วยการทำความเข้าใจการปฏิบัติงานและข้อควรระวังในแต่ละขั้นตอน บริษัทต่างๆ จึงสามารถบำรุงรักษาอุปกรณ์และจัดการกระบวนการผลิตได้ดียิ่งขึ้น
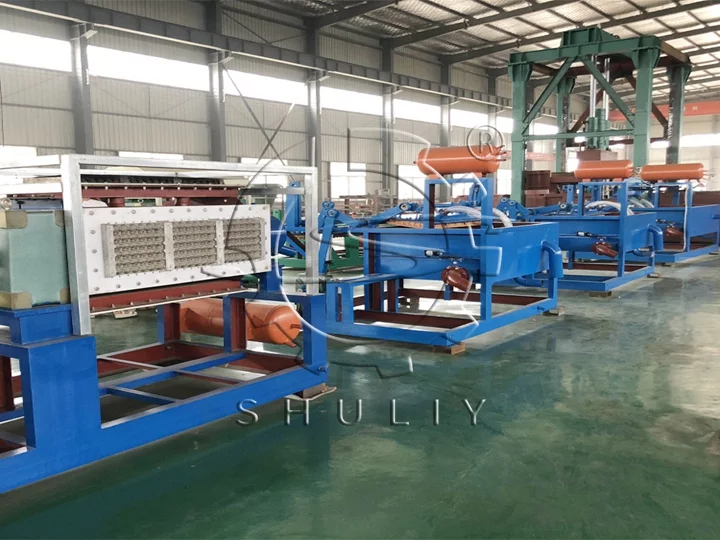
1. ขั้นตอนการเยื่อกระดาษ
ในขั้นตอนการผลิตเยื่อกระดาษ เศษกระดาษและน้ำจะถูกผสมในเครื่องผลิตเยื่อกระดาษเพื่อสร้างเยื่อกระดาษที่สม่ำเสมอ จากนั้นเยื่อนี้จะถูกประมวลผลผ่านการดำเนินการต่างๆ ในการปรับเยื่อและแหล่งจ่ายเพื่อให้ได้ความสม่ำเสมอและคุณภาพตามที่ต้องการ ขั้นตอนนี้มีความสำคัญอย่างยิ่งในการรับรองความสม่ำเสมอของเยื่อกระดาษ ซึ่งจำเป็นสำหรับกระบวนการขึ้นรูปในภายหลัง
2. ขั้นตอนการปั้น
ในระหว่างขั้นตอนการขึ้นรูป เยื่อกระดาษจะถูกดูดซับลงบนแม่พิมพ์โดยใช้แรงดันลบที่เกิดจากปั๊มสุญญากาศ จากนั้นเยื่อกระดาษจะถูกขึ้นรูปเป็นรูปร่างของถาดไข่โดยผ่านกระบวนการสุญญากาศและเป่าด้วยแรงดันบวก การทำงานที่แม่นยำนี้เป็นกุญแจสำคัญในการรับประกันว่าถาดไข่มีความหนาสม่ำเสมอและมีความแข็งแรงเพียงพอ
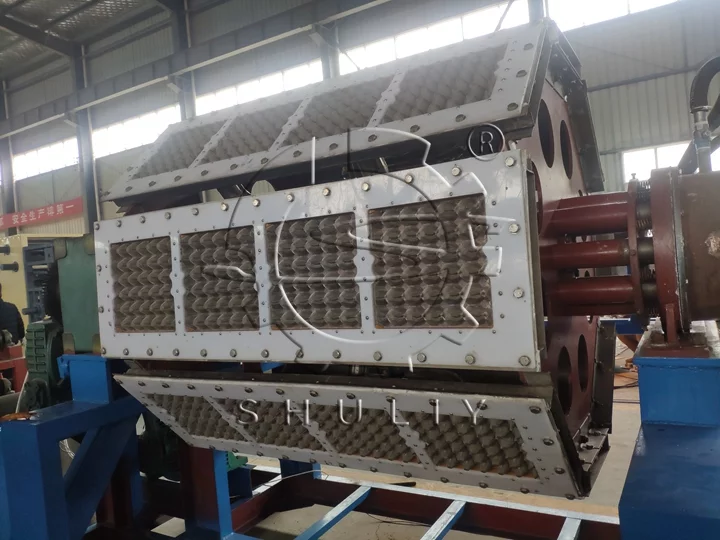
3. ขั้นตอนการอบแห้ง
ในขั้นตอนการอบแห้ง ถาดไข่ที่ขึ้นรูปจะถูกทำให้แห้งโดยใช้เครื่องอบแห้งเพื่อให้มั่นใจถึงความแข็งแรงและความทนทาน หลังจากการอบแห้ง ถาดไข่จะถูกนับ เรียงซ้อน และบรรจุหีบห่อสำหรับจัดเก็บและขนส่งโดยอัตโนมัติ การเลือกวิธีการทำให้แห้งและการกำหนดค่าอุปกรณ์ที่เหมาะสมสามารถเพิ่มประสิทธิภาพการผลิตได้อย่างมาก และรับประกันคุณภาพขั้นสุดท้ายของถาดไข่
ด้วยการทำความเข้าใจขั้นตอนการผลิตเหล่านี้ บริษัทต่างๆ จึงสามารถเพิ่มประสิทธิภาพกระบวนการผลิตและปรับปรุงประสิทธิภาพได้ การเลือกวิธีการทำให้แห้งและการกำหนดค่าอุปกรณ์ที่เหมาะสมตามความต้องการในการผลิตเฉพาะถือเป็นสิ่งสำคัญในการบรรลุผลลัพธ์สูงสุดในการผลิตถาดไข่
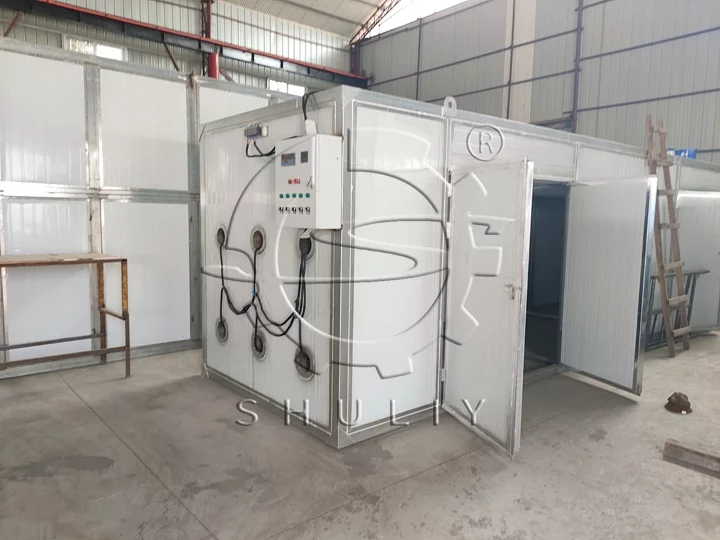
คำถามที่พบบ่อยเกี่ยวกับกระบวนการทำกล่องไข่
การมีสิ่งเจือปนในวัตถุดิบส่งผลต่อการผลิตถาดไข่อย่างไร
สิ่งเจือปนในวัตถุดิบในระดับสูงอาจทำให้คุณภาพและความแข็งแรงของถาดไข่ลดลง เพื่อแก้ไขปัญหานี้ จำเป็นอย่างยิ่งที่จะต้องใช้ตะแกรงสั่นเพื่อขจัดสิ่งเจือปนที่มีขนาดใหญ่กว่าก่อนที่จะเกิดการก่อตัวของเยื่อกระดาษ
ปัญหาการสึกหรอทั่วไปของแม่พิมพ์เครื่องทำถาดไข่คืออะไร และจะจัดการได้อย่างไร
โดยทั่วไปแล้ว การสึกหรอของเชื้อราจะมีน้อยมาก ในการจัดการการสึกหรอที่อาจเกิดขึ้นและรับรองความต่อเนื่องในการผลิต ให้พิจารณาซื้อชุดแม่พิมพ์เพิ่มเติม ด้วยวิธีนี้ คุณสามารถเปลี่ยนแม่พิมพ์ที่ชำรุดได้อย่างรวดเร็วและรักษาประสิทธิภาพการผลิตได้
เครื่องจักรเพียงเครื่องเดียวสามารถผลิตถาดไข่ทั้งแบบมาตรฐานและแบบสั่งทำพิเศษได้ และการเปลี่ยนแม่พิมพ์ทำงานอย่างไร
ใช่ เครื่องจักรเพียงเครื่องเดียวสามารถผลิตถาดทั้งแบบมาตรฐานและแบบสั่งทำได้โดยเพียงแค่เปลี่ยนแม่พิมพ์ สำหรับรูปทรงที่กำหนดเอง อาจจำเป็นต้องใช้อุปกรณ์เพิ่มเติม เช่น เครื่องรีดความร้อน การเปลี่ยนแปลงแม่พิมพ์ทำได้ตรงไปตรงมา ช่วยให้เกิดความคล่องตัวในการผลิต
การใช้เครื่องจักรผลิตถาดไข่ของคุณมีข้อดีอย่างไรเมื่อเปรียบเทียบกับคู่แข่ง
เครื่องจักรของเราใช้วัสดุเหล็กมาตรฐาน ทำให้มีความแข็งสูงและอายุการใช้งานยาวนาน ระบบอบแห้งมีโครงสร้างสแตนเลสเพื่อความทนทานและทนต่อการกัดกร่อน นอกจากนี้ เครื่องจักรของเรายังใช้ผ้าฝ้ายฉนวน 100% เพื่อกักเก็บความร้อนได้อย่างมีประสิทธิภาพและลดการใช้เชื้อเพลิง
บทสรุป
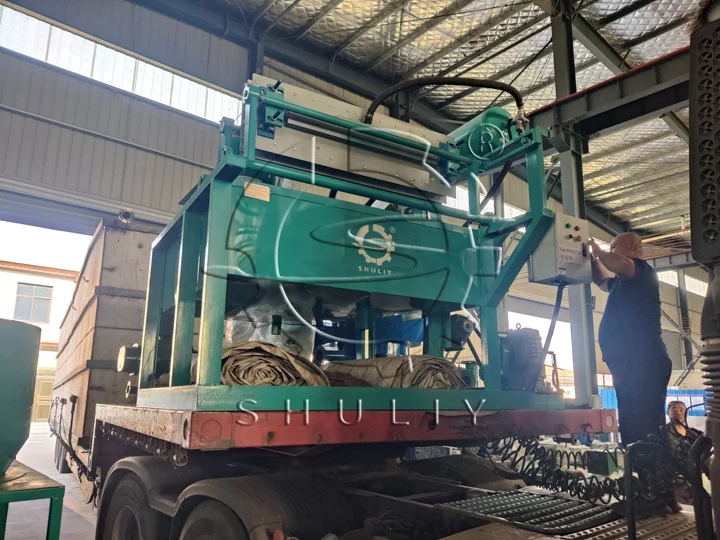
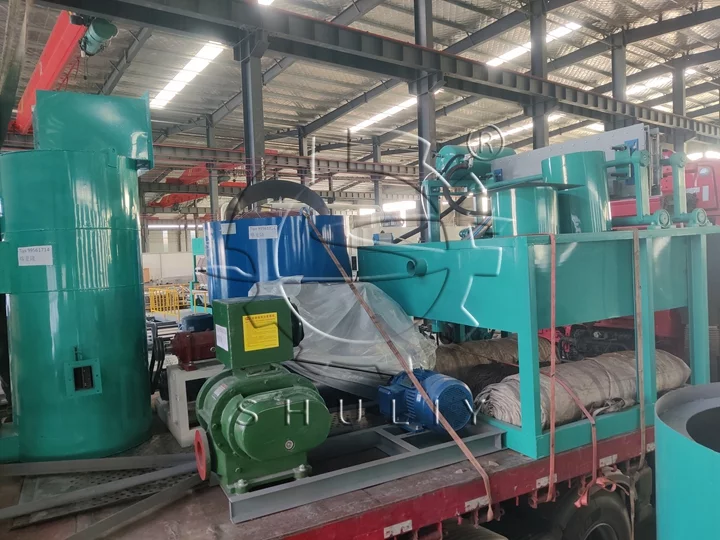
โดยการเลือกวัตถุดิบอย่างรอบคอบ, ปรับแต่งการกำหนดค่าของอุปกรณ์และกระบวนการผลิต, และปรับปรุงการจัดการบุคลากรและการบำรุงรักษาอุปกรณ์, บริษัทต่างๆ สามารถปรับปรุงประสิทธิภาพและคุณภาพของ การผลิตถาดไข่ ได้อย่างมีนัยสำคัญ.
ในสภาพแวดล้อมของตลาดที่มีการแข่งขันสูง มาตรการเหล่านี้จะช่วยให้บริษัทต่างๆ สามารถตอบสนองความต้องการของลูกค้าได้ดีขึ้น และเพิ่มความสามารถในการแข่งขันในตลาด หากคุณสนใจสายการผลิตถาดไข่หรือเครื่องจักรเฉพาะของเรา โปรดติดต่อเรา เราจะมอบโซลูชั่นที่ดีที่สุดตามความต้องการของคุณ