В марте мы продали машину для производства яичных поддонов на 1500шт/ч упаковочной компании во Франции. Клиент планировал создать внутреннюю производственную линию для экологически чистых яичных поддонов, используя отходы бумаги в качестве сырья.
Наша команда в Shuliy предоставила полное решение — от настройки оборудования до технической поддержки — помогая клиенту реализовать эффективное и устойчивое производство подносов.
История клиента
Французский клиент является региональным поставщиком упаковочных решений для птицеводства. С учетом растущего спроса на биоразлагаемую упаковку, они решили инвестировать в полуавтоматическую линию по производству яичных поддонов, чтобы снизить свои затраты и получить больший контроль над качеством продукции и сроками поставки.
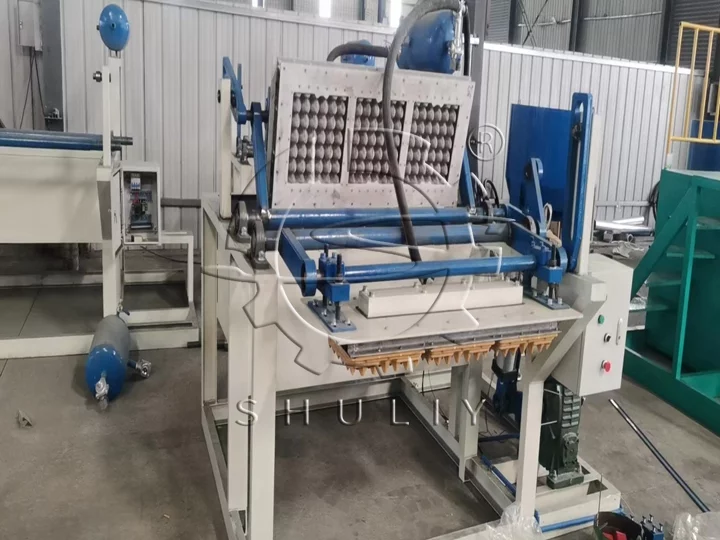
Требования клиента к машине для производства яичных лотков
- Производительность: 1500 шт/ч
- Сырьё: Отходы бумаги и картона
- Система формовки: Легкость в эксплуатации и высокая стабильность
- Метод сушки: Поддержка естественной сушки в связи с планировкой цеха
- Конфигурация питания: 380В / 50Гц в соответствии с французскими стандартами
- Дополнительные функции: Индивидуальная настройка форм и опция штабелера
Решение, предоставленное нашему клиенту
После оценки пространства завода клиента и его производственных потребностей, мы рекомендовали нашу машину для производства яичных поддонов на 1500шт/ч, оснащенную:
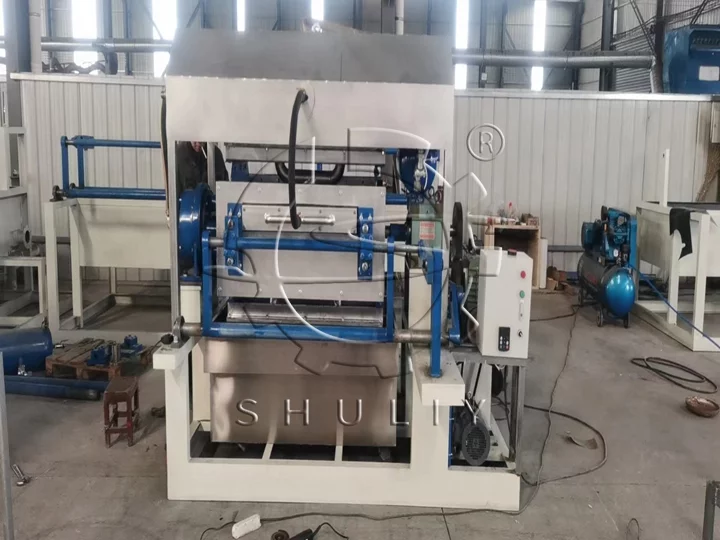
- 4-сторонним ротационным формовочным станком, способным обеспечивать стабильный выход с низким потреблением труда
- Системой пульпирования, включая гидравлический пульпер, рифинер пульпы и резервуар для хранения пульпы для обеспечения постоянного качества
- Методом естественной сушки, по предпочтению клиента, для снижения затрат на энергию
- Индивидуальные алюминиевые формы, адаптированные под стандартные 30-ячеечные яичные поддоны
- Опциональный автоматический штабелер для оптимизации процесса упаковки
- Все компоненты настроены для французской электросети 380В/50Гц.
Чтобы обеспечить плавный старт, мы предоставили видео по эксплуатации машин, инструкции по установке и удаленную помощь в реальном времени на английском языке.
Результаты и прогноз
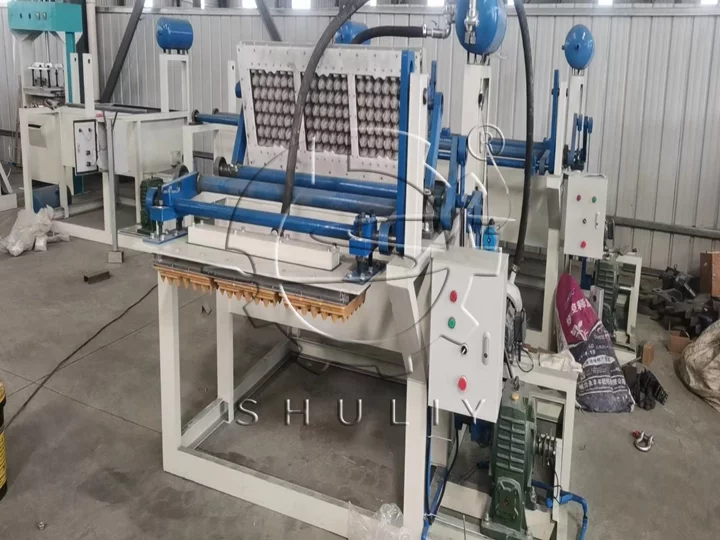
Благодаря успешной настройке, клиент теперь производит более 12 000 поддонов за 8-часовую смену, удовлетворяя местный спрос при сниженных затратах на упаковку и более быстром сроке доставки. Воодушевленный этой производительностью, клиент планирует увеличить свою производственную линию на следующем этапе.